ULTRASONIC WELDING
JOINING METALS WITH PRECISION
In the industrial world, the quest for efficient, precise and environmentally friendly joining methods is ongoing. Among these methods, ultrasonic welding has emerged as a powerful technique, offering a myriad of advantages over conventional methods like adhesive bonding or gas welding.
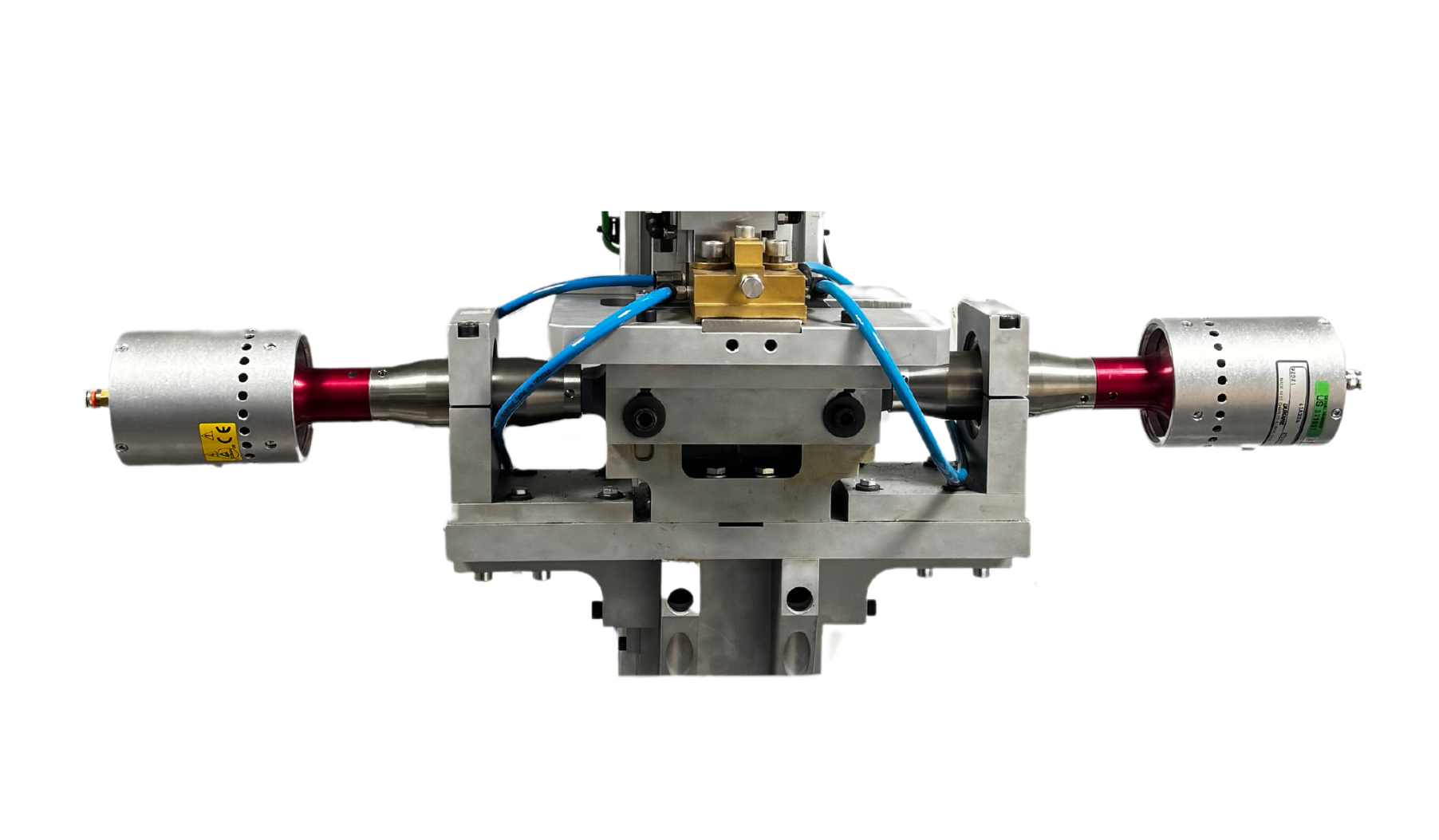
TECHNAX ultrasonic welding head
The ultrasonic welding process operates on the principle of converting high-frequency electrical energy into high-frequency mechanical energy. This mechanical energy manifests as reciprocating longitudinal motion, generating frictional heat at the interface.
This localized heat leads to a melt at the joining surfaces. Unlike traditional welding methods that rely on high temperatures, ultrasonic welding of metals is a cold welding process.
Ultrasonic waves are used to join metal parts, generating minimal heat except at the weld spot.
Vibrations resulting from the ultrasonic process are transmitted through a sonotrode, inducing movements at the weld interface while an anvil holds the components in place.
Friction generated at the interface leads to plastic deformation, enabling the materials to be joined without melting. This process is particularly suited for welding thin metals, films and wires, ensuring precise and reliable results.
BENEFITS
Speed and Precision : materials are melted and joined in split seconds with precise control over welding parameters.
Consistent Quality : advanced control technology ensures reproducible and appealing results, vital for applications requiring high precision.
Flexibility and Environmentally Friendly : ultrasonic welding can be adapted to various materials and shapes while being clean, energy-efficient and producing minimal waste.
Cost Efficiency : short process cycle times, low energy consumption and the elimination of additional tools or additives make ultrasonic welding a cost-effective process.
Strength and Safety : ultrasonic welding results in strong, visually flawless connections without damaging the metals, ensuring safety and reliability.
50mm2 copper cable on 4mm copper busbar
TECHNAX SOLUTIONS
Ultrasonic welding is suitable for joining similar and dissimilar metals, with a focus on non-ferrous metals such as aluminium, silver, copper and nickel. Applications range from battery and cable connections in the automotive and electronics industries to various electrical and mechanical components.
TECHNAX can perform process feasibility and validation tests in its welding laboratory. According to customer requirements, TECHNAX will support and offer the best industrial solutions for better productivity and long life-time of the equipment.
ULTRASONIC WELDING ASSEMBLY EXAMPLES
ULTRASONIC WELDING PROJECTS
Ultrasonic welding equipment